Common locations of oil leakage in skid-mounted fuel station and emergency treatment guide
First of all, we must emphasize that oil leakage during the operation of skid-mounted fuel station is a very dangerous situation with very serious safety hazards, and emergency treatment measures must be taken. This is mainly because oil is extremely volatile, causing the concentration of flammable substances in the air to increase, which can easily cause combustion or explosion and bring unimaginable consequences. Today, we will focus on explaining the preventive measures for oil leakage in skid-mounted fuel station and the emergency treatment guide after leakage from two aspects.
Common locations of oil leakage in skid-mounted fuel station
I. TOP5 high-risk leakage points (sorted by frequency)
High-risk locations are places that must be checked during daily routine inspections. During routine inspections, we must install basic requirements and never have a fluke mentality.
Location | Cause of leakage | Identification method | Key preventive measures |
1. Flange/valve sealing surface | Aging of gasket (rubber hardening due to temperature change), insufficient bolt preload (loosening due to vibration) | Spraying of foam leak detector, infrared thermal imaging to check temperature difference | Use of metal spiral wound gasket + hydraulic wrench (tightening according to ASME standard torque) |
2. Oil hose connector | Wear of quick connector O-ring, internal steel wire layer rupture caused by vehicle crushing of hose | Perform 1.25 times working pressure test every month | Install anti-collision guardrail, replacement cycle ¡Ü 2 years (HNBR material is required for ethanol gasoline environment) |
3. Tank weld/corrosion point | Electrochemical corrosion of underground tank outer wall (stray current), weld porosity defects (manufacturing problems) | Vacuum box detection (negative pressure 0.03MPa), ultrasonic thickness measurement | The outer wall of the tank is coated with polyurea anti-corrosion layer + sacrificial anode protection (replaced every 5 years) |
4. Liquid level meter probe seal | High-frequency vibration causes the gland seal to loosen, and the probe seal aluminum sleeve is corroded and perforated by sulfide | Oil odor concentration detector scans and observes the instrument data jump | Use a double-seal structure probe (inner PTFE + outer fluororubber) |
5. Emergency shut-off valve actuator | Valve stem seal packing failure (frequent action wear), solenoid valve coil overheating causes shell cracks | Perform emergency shutdown test within 0.5 seconds | Add valve grease every month, coil temperature <= 80 Celsius (install heat sink) |
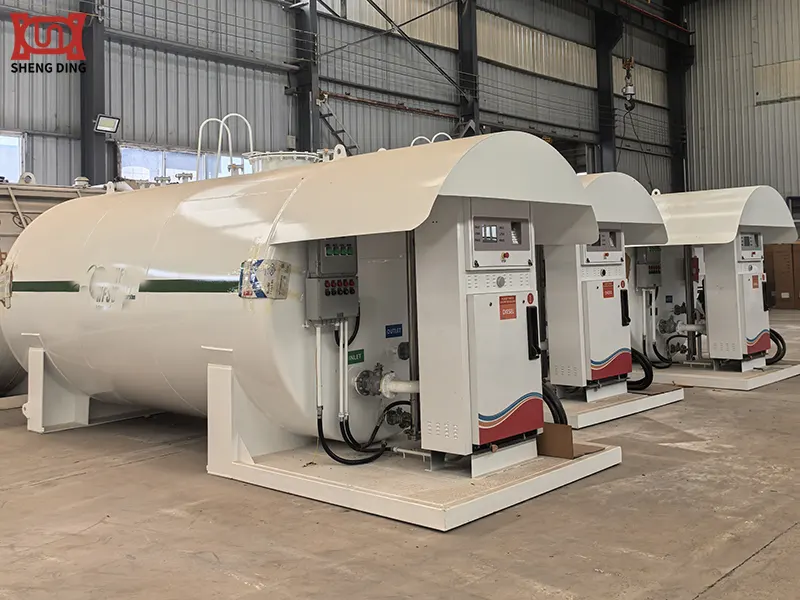
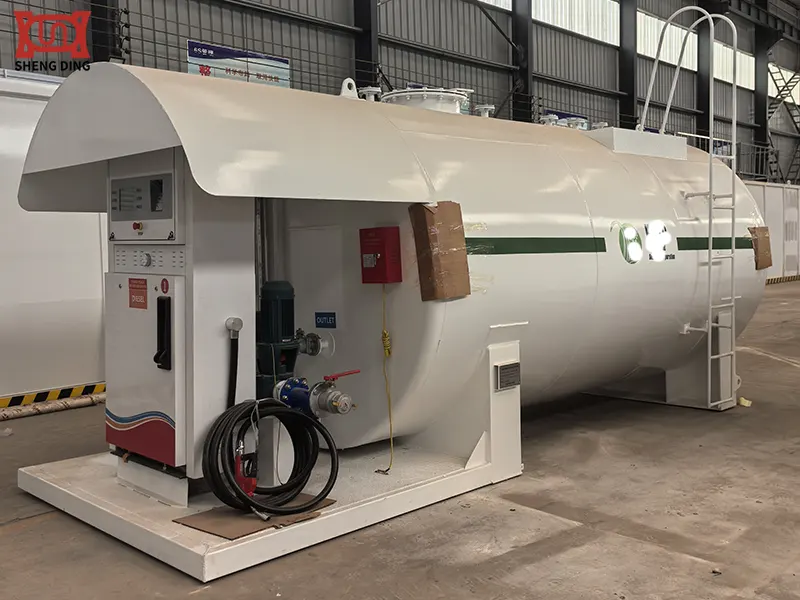
II. Hidden risk points (easy to be ignored but harmful)
Hidden risks are actually the most dangerous, because they are extremely easy to be ignored, and this position generally requires experienced managers to observe. Therefore, we must cultivate experienced managers in our daily management work.
1. Leakage in the interlayer of double-walled tanks.
- Problem: After the inner tank leaks, oil accumulates in the interlayer, corroding the outer tank and causing secondary leakage.
- Detection: Install interlayer vacuum pressure sensor ( > 5kPa alarm).
- Case: A station was fined 1.2 million yuan because 3 tons of gasoline leaked into the ground without monitoring the interlayer.
2. Condensate discharge valve of the vent pipe
- Problem: Condensate freezes and cracks the valve body in winter, and oil leaks after thawing.
- Solution: Use electric heating antifreeze valve (automatic start at 4 Celsius).
3. Oil discharge port ball valve seal
- Problem: Frequent plugging and unplugging of the oil discharge gun causes scratches on the valve seat.
- Maintenance: Apply silicone-based grease after each oil discharge, and replace the valve seat seal every year.
III. Leakage prevention technology upgrade plan
Technical means | Applicable parts | Effect | Cost reference |
Intelligent leakage monitoring system | Tank bottom/pipeline | 0.1L/h leak instant alarm (accuracy 10 times higher than industry standard) | $4,000/station |
Carbon fiber reinforced hose | Fuel dispenser pipeline | Rolling resistance increased by 3 times, life of 5 years | $150/meter |
Laser cladding repair | Tank corrosion point | After repair, the strength reaches 98% of the new product, avoiding the need for overall tank replacement | $5,000/place |
IoT bolt monitoring | Flange connection | Real-time display of bolt preload, automatic loosening warning | $30/piece |
IV. Regulatory mandatory testing requirements (avoid legal risks)
1. Annual inspection
- Storage tank: air tightness test (0.035MPa pressure maintenance for 30 minutes) + wall thickness detection (thinnest point >= 85% of original thickness).
- Pipeline: 0.4MPa pressure test (stable pressure for 1 hour without pressure drop).
2. Quarterly maintenance
- Replace all seals (perfluoroether rubber is recommended, chemical resistance is increased by 6 times)
- Clean the static grounding resistor (value <= 10 ohm)
The above are the locations and preventive measures for oil leakage in skid-mounted fuel station. As the operation and management personnel of gas stations, we must keep safety in mind. Do not deal with routine safety inspections. Only by fulfilling your duties can you have a safe production environment.
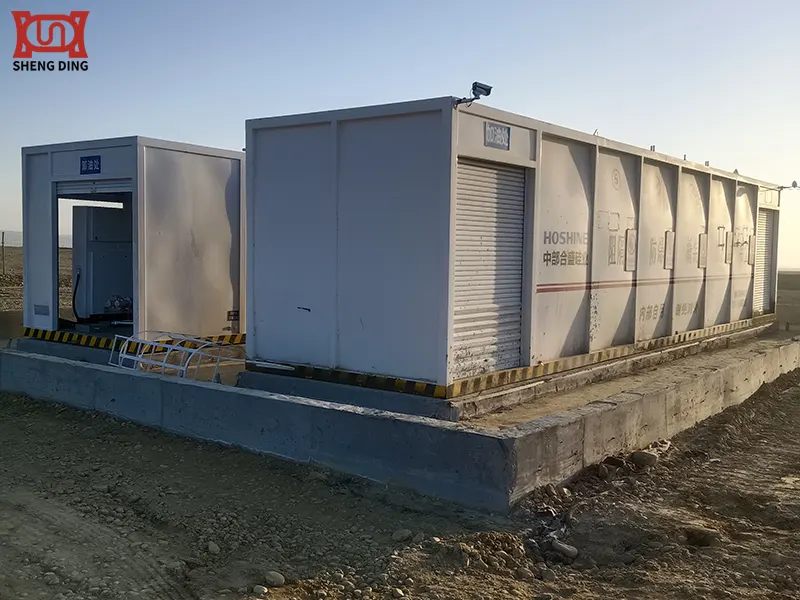
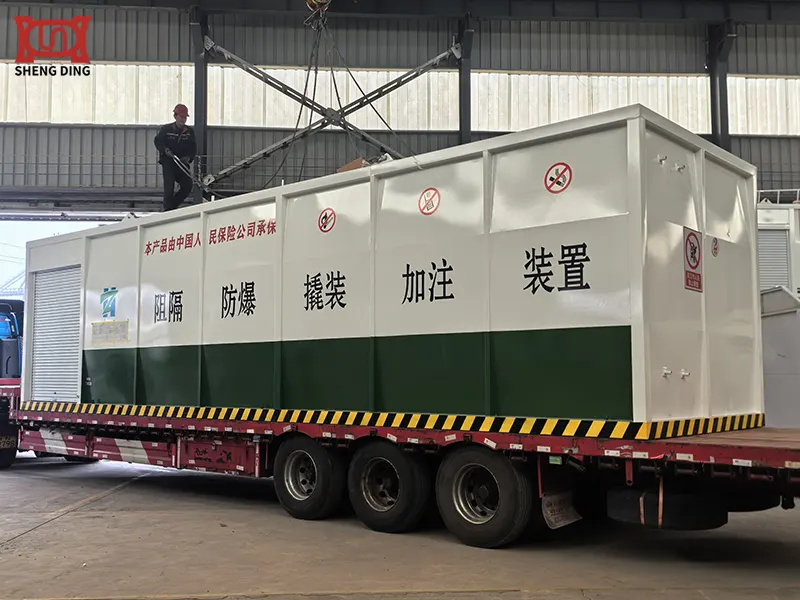
Emergency treatment guide for oil leakage in skid-mounted fuel station
I. Immediate action: emergency disposal procedures
1. Emergency shutdown and isolation
- Immediately stop all refueling operations, turn off the oil pump, and cut off the power supply (use explosion-proof switches).
- Evacuate personnel and vehicles on site, set up a warning zone of at least 50 meters, and prohibit ignition sources such as open flames, smoking, and mobile phones.
- If the leakage is large, call 119 fire and emergency environmental protection department immediately (if the oil has entered the soil or drainage system).
2. Control the source of the leak
- If the valve/interface leaks: tighten or replace the seal with explosion-proof tools (only when there is a slight leak and safety is ensured).
- If the tank/pipeline is broken: use oil-absorbing cotton and plugging glue for emergency absorption and covering (special chemical plugging glue is suitable for metal cracks).
- Contain and drain the oil leakage area: use sandbags to build embankments to prevent oil from flowing into the sewer or soil, and drain it to the emergency collection pit.
3. Adsorption and cleaning
- Use oil-absorbing felt and oil-absorbing particles to fully cover the oil stains (about 1.5kg of oil-absorbing cotton is required for 1 liter of oil). It is strictly forbidden to use water flushing!
- The surface of the contaminated soil must be immediately removed (depth >= 10cm) and placed in a leak-proof hazardous waste barrel.
II. Root cause investigation (professional testing required)
Common leakage points | Possible causes | Detection methods |
Tank weld/corrosion points | Material aging, welding defects, underground corrosion | Ultrasonic thickness measurement, vacuum box detection |
Valve/flange interface | Sealing ring aging, bolt loosening | Gas sniffer, foam leak detector |
Emergency shut-off valve failure | Sensor failure, mechanical jamming | Functional test + pressure test |
Damaged oil hose | Cracks, rolling damage | Visual inspection + pressure test |
III. Subsequent compliance treatment
1. Hazardous waste disposal
- Contaminated oil-absorbing cotton and soil shall be treated as HW08 hazardous waste, and contact qualified units (who must hold a "Hazardous Waste Operation License") for transfer, and retain the transfer form.
- Cleaning wastewater must be included in the oily wastewater system for treatment, and direct discharge is prohibited.
2. System maintenance and acceptance
- Entrust a unit with GA pressure vessel qualification to conduct air tightness test on the storage tank (0.03MPa pressure maintenance for 30 minutes without pressure drop).
- Replace all O-rings and gaskets (oil-resistant fluororubber is recommended).
- After passing the third-party inspection, submit the inspection report to the Emergency Management Bureau for record.
3. Environmental remediation
- If the soil is polluted, drilling sampling analysis (depth 3-5 meters) is required, and a repair plan is formulated in accordance with the "Soil Pollution Prevention and Control Law".
IV. Preventive measures upgrade
- Install secondary protection: add anti-leakage trays (volume >= 110% of tank capacity) in the storage tank area, and install leakage monitors (real-time alarm).
- Strengthen inspections: check the status of flanges and valves every day; perform vacuum pressure tests on storage tanks every month.
- Emergency drills: Conduct oil leakage emergency drills every quarter, focusing on training the use of plugging tools and hazardous waste disposal procedures.
- Important reminder: According to the "Regulations on the Safety Management of Hazardous Chemicals", failure to report a leak in a timely manner may result in a fine of 100,000 to 500,000 yuan. If a fire or pollution is caused by oil leakage, the person responsible will bear criminal responsibility!
Today, I have explained to you in detail and thoroughly the situation of oil leakage in skid-mounted fuel station. I hope that the above explanation can be of some help to you when you operate skid-mounted fuel station in the future.
Written by
TAIAN SHENGDING METAL CONTAINER MANUFACTURING CO., LTD.
Editor Wang
www.self-bunded-tank.com
WhatsApp:+86 152 5486 3111
Email:shengdingtank@126.com
- WhatsApp
- E-MailE-Mail:shengdingtank@126.com
- WeChatWeChat:15254863111