Common methods for double wall tank leakage detection and their advantages and disadvantages
With the improvement of social production safety standards, the oil storage industry has basically adopted safer double-layer oil tanks. It has not only made great technical improvements in preventing oil leakage, but also made certain contributions to protecting oil quality. However, sometimes due to some external forces or environmental factors, it will cause leakage. This phenomenon is very dangerous. We must use technology to find the leakage point and then take certain measures. Today we will explain to you the common methods of double wall tank leakage detection and their advantages and disadvantages.
Detecting leakage in double wall tank is a vital environmental protection and safety measure. The design of the double-layer tank (there is a continuous gap space between the inner tank wall and the outer tank wall) is itself a leakage monitoring system, and its main purpose is to detect leakage of the inner or outer tank wall early and reliably.
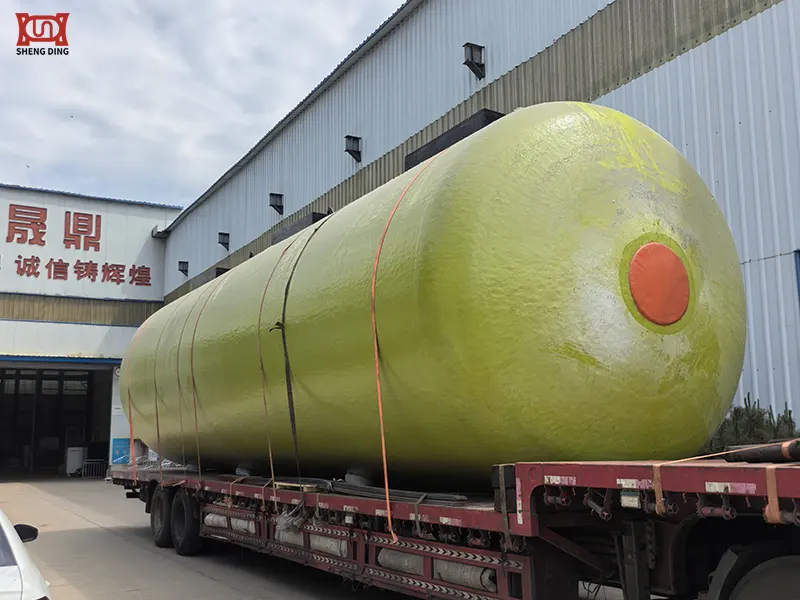
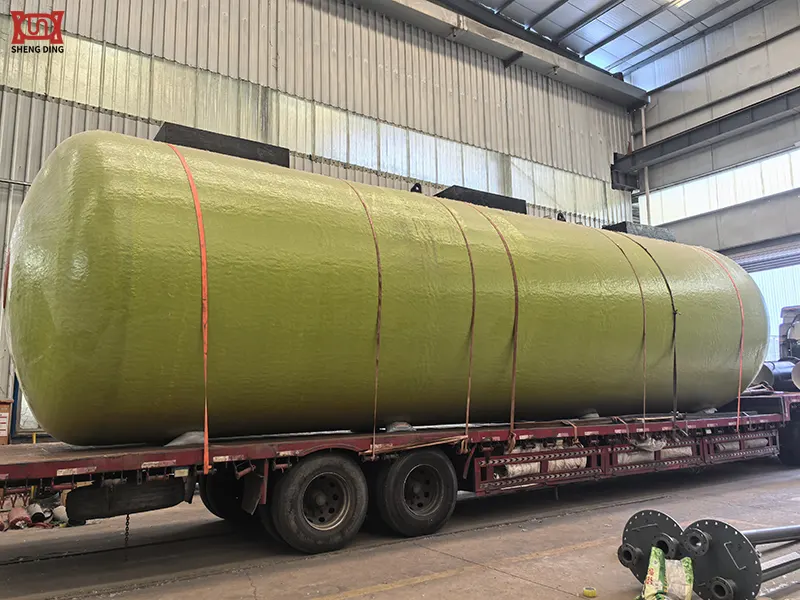
The following are the main methods and technologies for detecting leakage in double wall tank:
I. Continuous monitoring system for interstitial space (the most common and core method)
This is the core advantage of double-layer tanks, which are usually equipped with real-time online monitoring equipment:
1. Pressure monitoring method:
- Principle: Apply a certain positive pressure to the interstitial space (usually air or inert gas) and continuously monitor pressure changes.
- Detection of leakage:
- Inner layer leakage: If the inner tank wall is broken, the liquid (oil) in the tank will penetrate into the interstitial space, causing the pressure to increase.
- Outer layer leakage: If the outer tank wall is broken (or the tank bottom leaks), the gas in the interstitial space will leak into the external soil or water, causing the pressure to drop.
- Advantages: Fast reaction speed, can distinguish inner or outer layer leakage, and the technology is relatively mature.
- Disadvantages: The sensitivity to small leaks may not be as good as the vacuum method, and it is greatly affected by temperature changes (temperature compensation is required).
2. Vacuum monitoring method:
- Principle: Establish and maintain a certain vacuum degree (negative pressure) in the interstitial space, and continuously monitor the changes in vacuum degree.
- Leak detection:
- Inner layer leakage: When the inner tank wall ruptures, liquid or air enters the gap space, resulting in a decrease in vacuum (pressure rise).
- Outer layer leakage: When the outer tank wall ruptures, external air or water is sucked into the gap space, which also results in a decrease in vacuum (pressure rise).
- Advantages: Usually more sensitive to tiny liquid leaks (liquid entering the vacuum space will produce obvious signals).
- Disadvantages: Generally, it is not possible to directly distinguish whether it is an inner or outer layer leak (it needs to be combined with other inspections), the system is relatively complex, and the cost may be slightly higher.
3. Liquid media sensor method:
- Principle: Fill the gap space with a specific liquid (conducting liquid) and install a liquid level sensor at the lowest point (liquid collecting tank).
- Leak detection:
- Inner layer leakage: The inner tank wall ruptures, and the oil enters the gap space. Since the density of the oil is usually less than that of the guiding liquid, it will float above the guiding liquid and flow into the collecting tank, triggering the liquid level sensor alarm.
- Outer layer leakage: When the outer tank wall ruptures, the guiding liquid will leak into the external soil, causing the guiding liquid level in the gap space to drop, and the sensor will also alarm.
- Advantages: It can detect very small liquid leaks, and the change in liquid level is a clear leak signal.
- Disadvantages: The installation is relatively complicated (need to fill the guide liquid), and the guide liquid status (such as liquid level, whether it is contaminated, frozen, etc.) needs to be checked and maintained regularly. It is usually impossible to distinguish between internal and external layer leaks, and the response speed may not be as fast as the pressure/vacuum method. The guide liquid leakage itself may also cause pollution (environmentally friendly guide liquid needs to be selected).
4. Cable/fiber optic sensing method
- Principle: Lay special sensing cables or optical fibers in the interlayer space. When the oil contacts the cable/fiber optic, its electrical properties (such as resistance, capacitance) or optical properties (such as light signal attenuation) will change.
- Detecting leaks: Monitoring changes in cable/fiber optic properties can locate the approximate location of the leak.
- Advantages: Ability to locate the leak point, which helps to quickly repair.
- Disadvantages: The system cost is high, the installation is relatively complex, and there are requirements for sensor layout.
II. Periodic detection method (as a supplement or verification of continuous monitoring)
1. Liquid medium method (periodic detection version):
The gap space is filled with guide liquid, but it is not equipped with a continuous liquid level sensor. It is necessary to check whether the liquid level in the sump has changed (increased or decreased) manually (observation well, measuring rod) regularly (such as monthly).
- Advantages: Relatively low cost.
- Disadvantages: It is not real-time, relies on manual regular inspection, and may miss the exact time when the leak occurs.
2. Sensor method (periodic detection version):
Install a liquid sensor probe in the gap space, but do not perform continuous monitoring. It is necessary to use a handheld reader to connect to the sensor to read the data regularly (such as monthly) to check whether there is a signal of liquid presence.
- Advantages: can detect small liquid leaks.
- Disadvantages: non-real-time, relying on manual regular inspection.
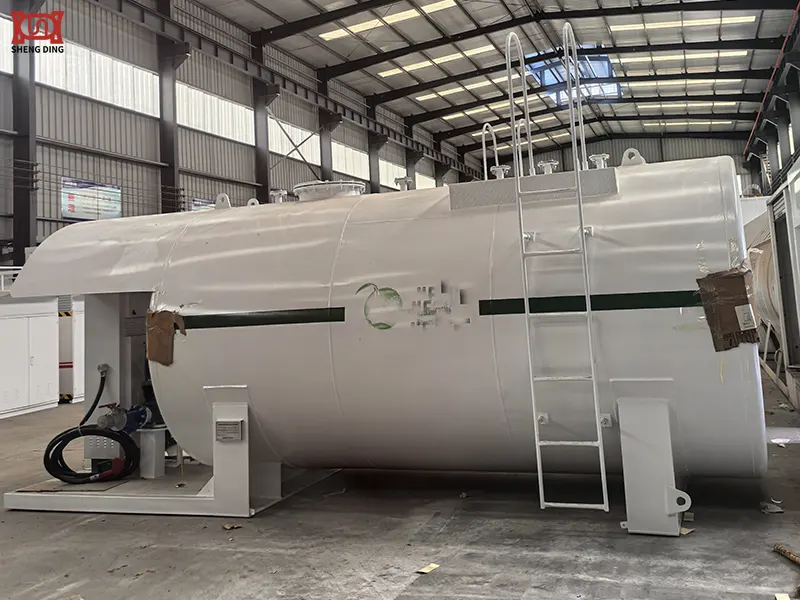
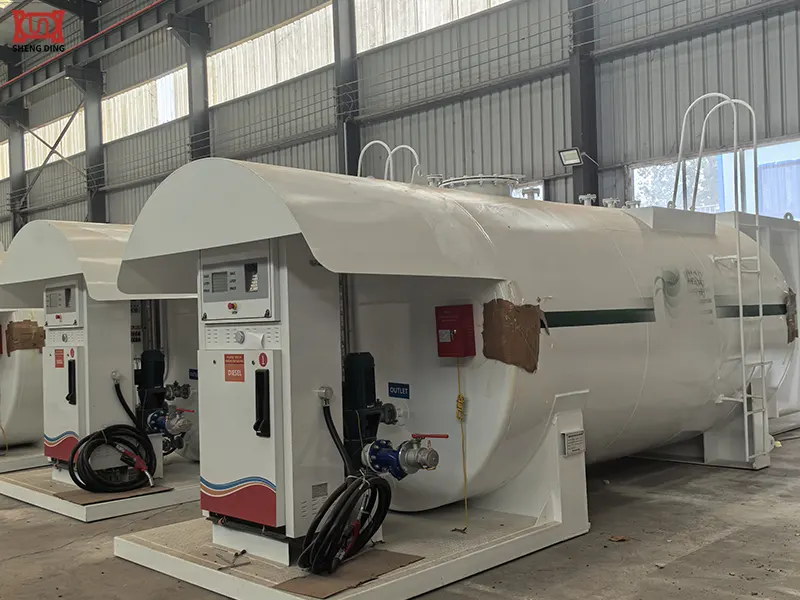
III. Other monitoring and management measures
1. Oil inventory monitoring:
Although it is not possible to directly detect gap leakage in double-layer tanks, inventory control (SIR) combined with accurate level meters (such as magnetostrictive probes) is an important means to detect whether the tank as a whole is leaking (for example, the inner layer leaks directly into the soil, but does not trigger the gap monitoring system). This is one of the mandatory detection methods required by regulations. Any persistent and unexplained inventory loss may be a sign of leakage.
2. Visual inspection:
Regularly check the oil tank and its accessories (manhole covers, pipeline joints, monitoring ports, etc.) for abnormal conditions such as oil pollution, corrosion, damage, etc. Check whether there is liquid in the secondary sealing pool.
3. System function test:
Regularly (usually at least once a year) perform functional tests on the continuous monitoring system to simulate leakage signals and ensure that the alarm function is normal.
4. Record keeping:
Completely and accurately record all monitoring data, alarm information, inspection results, test reports and maintenance records.
IV. Considerations for selecting detection methods
- Regular testing: Regulations usually require regular leakage detection of double wall tank (such as monthly, quarterly or annually, the specific frequency depends on regulations, oil tank type and detection method). Continuous monitoring systems (such as vacuum/pressure, liquid level sensors) themselves also require regular functional testing (usually once a year).
- Automatic shutdown: For high-risk areas (such as water source protection areas), regulations may require that the system automatically shut down the oil supply or trigger an alarm when a leak is detected.
- Record keeping: All test results, test reports and maintenance records must be properly kept for inspection by regulatory agencies.
- Standard compliance: Installation, testing and maintenance must comply with relevant national and local standards (such as China's GB series standards, the United States' STI RP100, PEI RP900, Europe's EN 13160, etc.).
- Sensitivity: How small a leak needs to be detected.
- Reliability: The probability of false alarms and missed alarms of the system.
- Distinguishing the leak location: Can it distinguish between inner and outer leaks.
- Response time: The time from the occurrence of a leak to the alarm.
- Installation and maintenance costs: initial investment and long-term maintenance costs.
- Operational convenience: the complexity of daily operation and maintenance.
- Environmental adaptability: whether it is suitable for local temperature, humidity, geology and other conditions.
Summary
Continuous monitoring (pressure method, vacuum method, continuous liquid media sensor method) is the first choice and core of double-layer oil tank leakage detection, which can provide real-time or near real-time leakage alarm.
Periodic detection methods (periodic liquid media method, periodic sensor method) can be used as a low-cost solution or supplementary means, but there is a monitoring blind period.
Oil inventory control is an important leak detection method independent of double-layer gap monitoring and is a mandatory requirement of regulations.
Comprehensive management (visual inspection, functional testing, record keeping) is essential to ensure the long-term and effective operation of the entire system.
Strongly recommended:
- 1. Strictly comply with local regulations on the specific requirements for double-layer oil tank leakage detection.
- 2. Select certified and reliable monitoring equipment and systems.
- 3. Installation, commissioning, calibration and maintenance by professionals.
- 4. Establish a complete daily inspection, regular testing and maintenance system, and keep complete records.
- 5. Once the monitoring system alarms, the oil tank must be immediately deactivated, and the emergency plan must be followed for investigation, confirmation and disposal to prevent the expansion of pollution.
The above are the common methods and advantages and disadvantages of double-layer oil tank leakage detection that we have compiled and published for everyone. I hope that the above explanation can be of some help to everyone when using double wall tank in the future. Oil leakage is a serious matter, so you must be careful to follow the relevant technical specifications. If necessary, you must consult a professional oil tank inspection service company or environmental protection department to design and implement the most appropriate leak detection plan based on your specific situation (oil tank type, storage medium, site environment, regulatory requirements, etc.).
Written by
TAIAN SHENGDING METAL CONTAINER MANUFACTURING CO., LTD.
Editor Wang
www.self-bunded-tank.com
WhatsApp:+86 152 5486 3111
Email:shengdingtank@126.com
- WhatsApp
- E-MailE-Mail:shengdingtank@126.com
- WeChatWeChat:15254863111